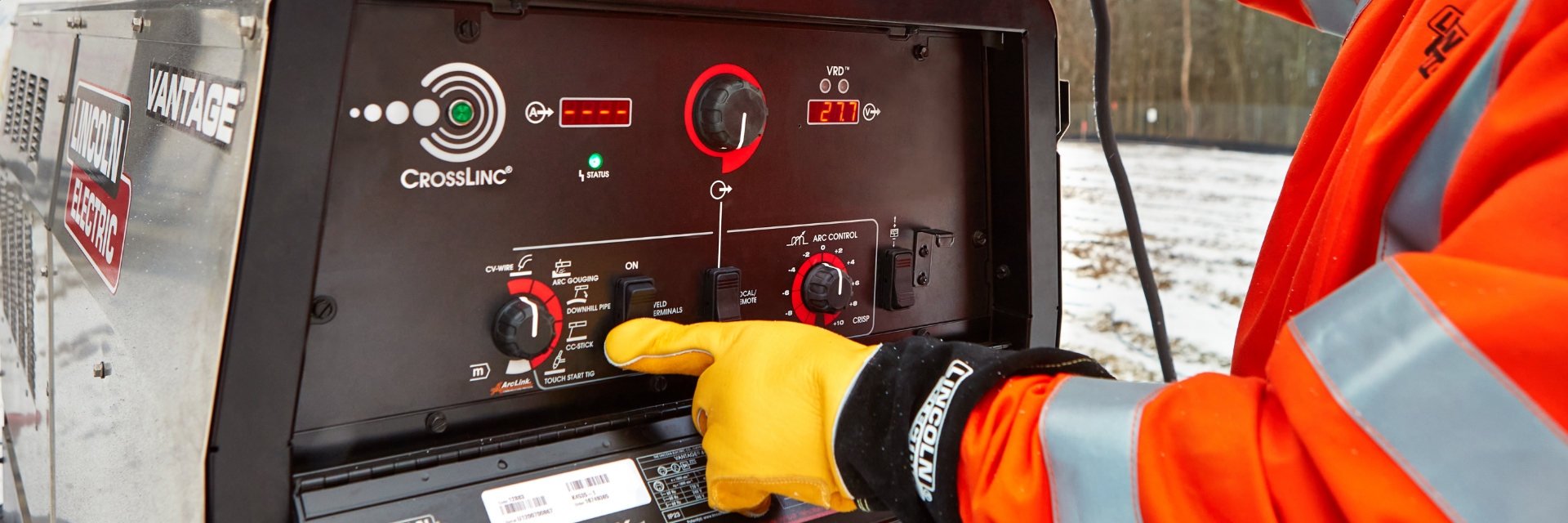
Solutions
VITALITY INDEX SUMMARY
Our Vitality Index is the percentage of new standard product revenues in the past five years, divided by the company's total revenues over the same period. New products exclude customized automation sales.
A Vitality Index is a common metric used to measure the effectiveness of a company's R&D innovation efforts. A high Vitality Index indicates that a company is effectively using its R&D resources to develop new products that are driving revenue growth. As a leader in welding technology and safety, our newest products are designed to make a positive impact, including automation products and enhanced software solutions. We consider our customers' sustainability goals in our product offerings, and strive to improve product material and energy efficiency, as well as safety. Many of our new products also deliver sustainability benefits. Several are highlighted below.
AUTOMATION: POSITIONING FOR THE FUTURE
Lincoln Electric continues to develop an array of equipment and systems to remove inconsistencies from the welding process and maximize safety and efficiency. Our automation story is one of constant innovation, with the goal of providing industry-leading tools suitable for manufacturers around the world. Lincoln Electric's unparalleled combination of experience, expertise and customer support gets automation processes online quickly and successfully.
- COLLABORATIVE ROBOTICS Welding “cobots” are automated welding solutions built to work safely alongside people. Their easy-to-use app enables users to program welds quickly and consistently.
- MECHANIZED EQUIPMENT Mechanized welding equipment includes seam tracking, positioners, manipulators, jaw chucks, motorized slides, manual slides, pipe support strands, turning and idle rolls, and accessories for various applications.
- ROBOTIC WELDING SYSTEMS From simple to advanced applications, these systems are designed to help decrease manufacturing costs, increase weld quality, improve welding productivity, and enhance your working environment.
- AUTOMATED CUTTING SYSTEMS Lincoln Electric's automated CNC cutting solutions encompass every application, including plasma cutting and motion control, tube and automated pipe cutting, structural steel cutting and more.
- ROBOTIC GRINDING SYSTEMS The OmniClean™ robotic grinding systems are pre-engineered to help improve weld grind consistency and efficiency in various applications.
- ROBOTIC LASER SYSTEMS The Laser-Pak® robotic laser systems are ideal for laser welding, cladding, feature building, joining, brazing and additive manufacturing applications.
- AUTOMATED POSITIONERS Positioners adapt part and robot orientations for a range of applications, including welding, cladding, laser, material handling, grinding and cutting.
- SPRAY AND DIE CASTING/FOUNDRY/FORGING EQUIPMENT Serving the die-casting, foundry and forging industries for more than a half-century, Lincoln Electric Automation of Columbus Ohio (formerly Rimrock) mechanized and robotic ladles, reciprocators, spray atomizers and spray wands promote safety and efficiency in the work environment.
- AUTOMATED MATERIAL HANDLING Lincoln Electric teams are experts in the concept and creation of custom high-capacity automated vehicles with the highest positioning accuracy and repeatability for large-scale material handling applications.
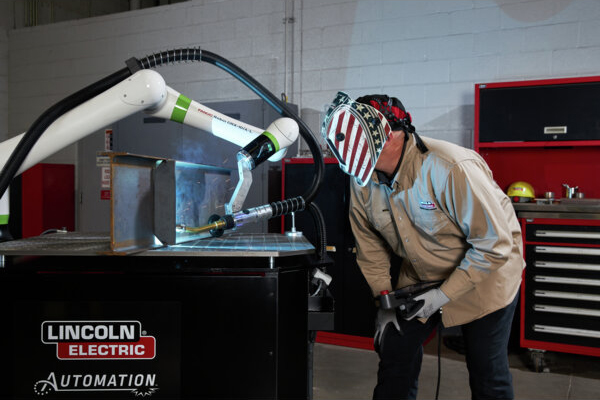
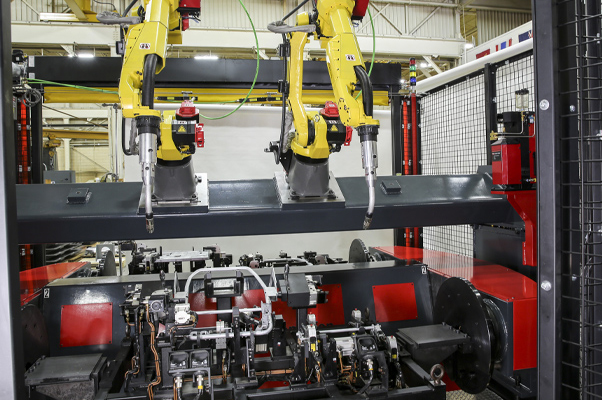
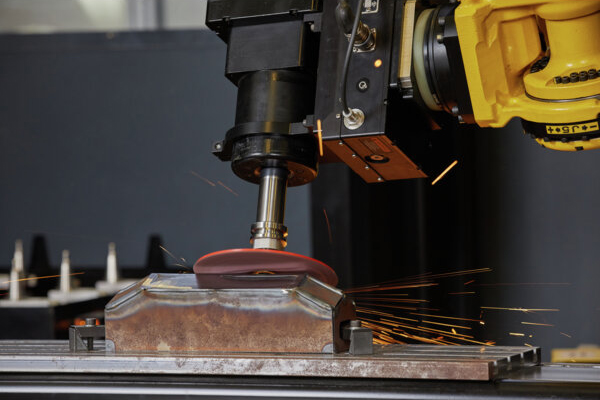
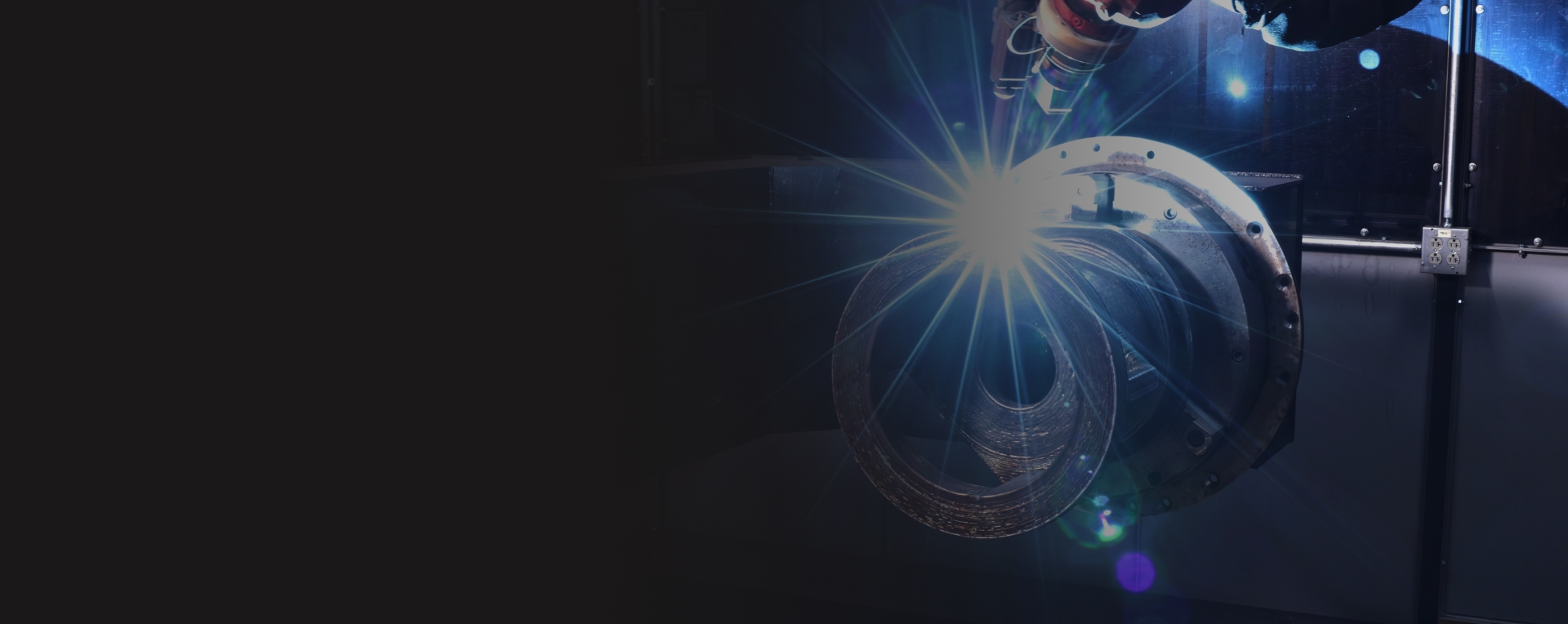
LINCOLN ELECTRIC ADDITIVE SOLUTIONS MAKES BIG PARTS IN LESS TIME
Lincoln Electric Additive Solutions gives your business a big advantage over castings, forgings and other traditional manufacturing processes with the fast delivery of new and replacement parts and tooling.
With the largest 3D metal printing capacity in North America, we can expedite production for large industrial parts for your application and industry.