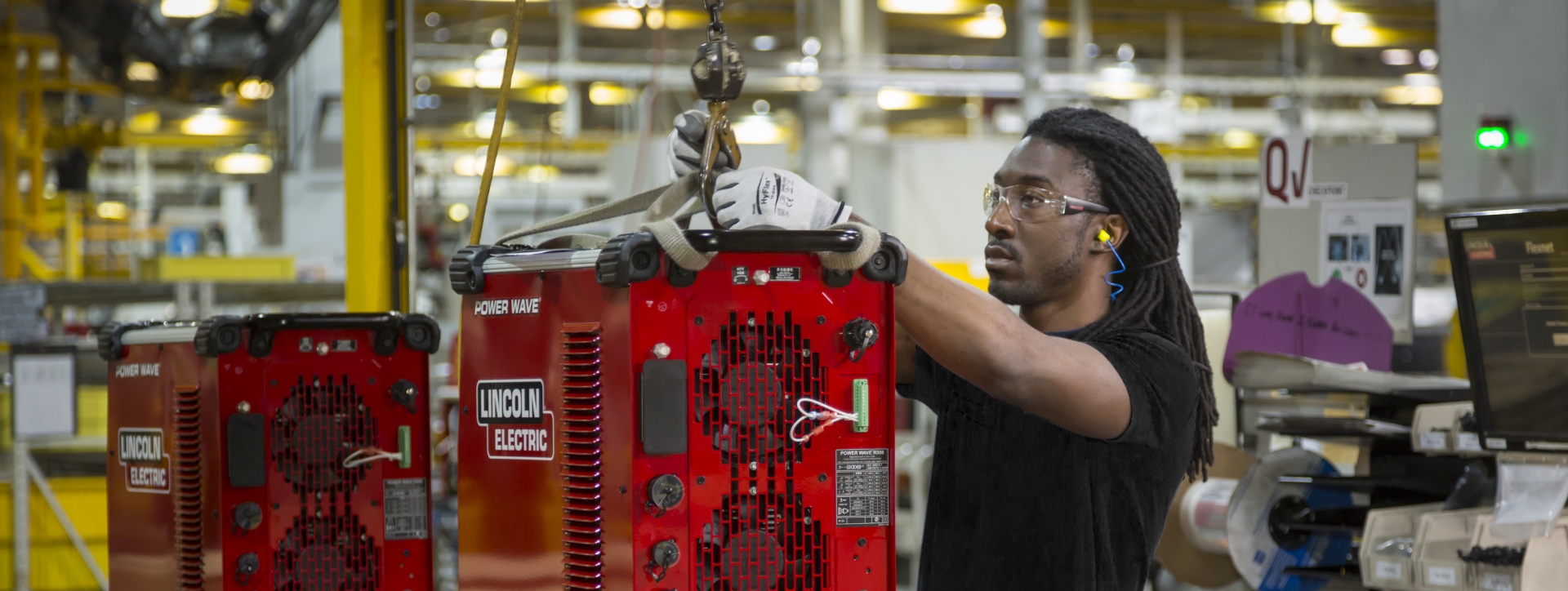
Operational
SAFETY
Safety Performance
We monitor and measure several safety metrics across our operations, including Days Away, Restricted or Transferred Case Rate (DART), and Total Recordable Case Rate (TRCR), which measure the frequency of safety incidents that occur within our facilities
73%
Of all manufacturing sites and 100% of major manufacturing sites were ISO 14001 certified in 2023
31%
Of all manufacturing sites were also certified to the ISO 45001 standard for occupational health and safety
2018—2023 Safety Performance(1)
TRCR
38%
Reduction
Reduction
in Total Recordable Cases (TRCR)(1) (from 2018 to 2023)
DART
7.1%
Reduction
Reduction
in Days Away, Restricted, & Transferred (DART)(1) (from 2018 to 2023)
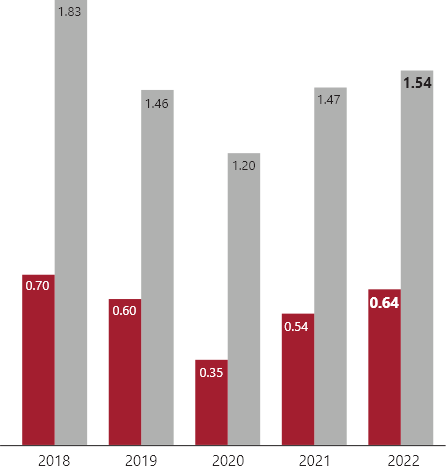
Annual data as of December 31 — end of each reporting year
- TRCR and DART are calculated per the U.S. OSHA definition for the Total Recordable Incident Rate (TRIR) and the Days Away, Restricted or transferred (DART) Rate. Which are calculatedper 100 full time employees.
Our management system approach to environmental, health, and safety (EHS) includes:
- EHS Policy and Global EHS Directives that establish the Company's standard expectations — which often exceed compliance obligations — for EHS performance across our operations.
- Training across a wide variety of safety topics, including peer-to-peer observations and interventions.
- Employee-led joint management safety committees that focus on improving our safety culture by identifying and addressing unsafe conditions, reinforcing safe acts, and instructing one-on-one safe work practices.
- Commitment to International Standards Organization (ISO) 14001 implementation at all major manufacturing locations.
- A focus on learning from events and near misses of all types that supports process redesign and improvement.
- Extensive auditing and regular monitoring of our safety performance, which enables accountability at all levels of the organization and assesses the health of the program.
- Award and recognition programs, including our annual Chairman's Awards for Safety, Environment and Sustainability Excellence, as well as a Safety Leadership Award for Plant/General Managers, Business Unit President Awards, citations for high-performing employees who make superior contributions to the business, and “Best Practice” designation for site-level projects that are innovative, impactful, and transferable across the enterprise.
EHS Best Practices
“Every year, facilities are invited to submit their best EHS projects of the year for the Annual Best Practices Contest.”
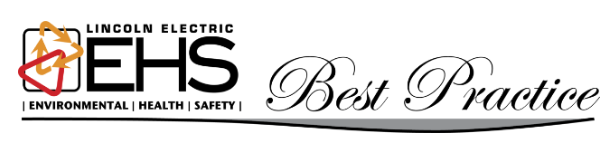