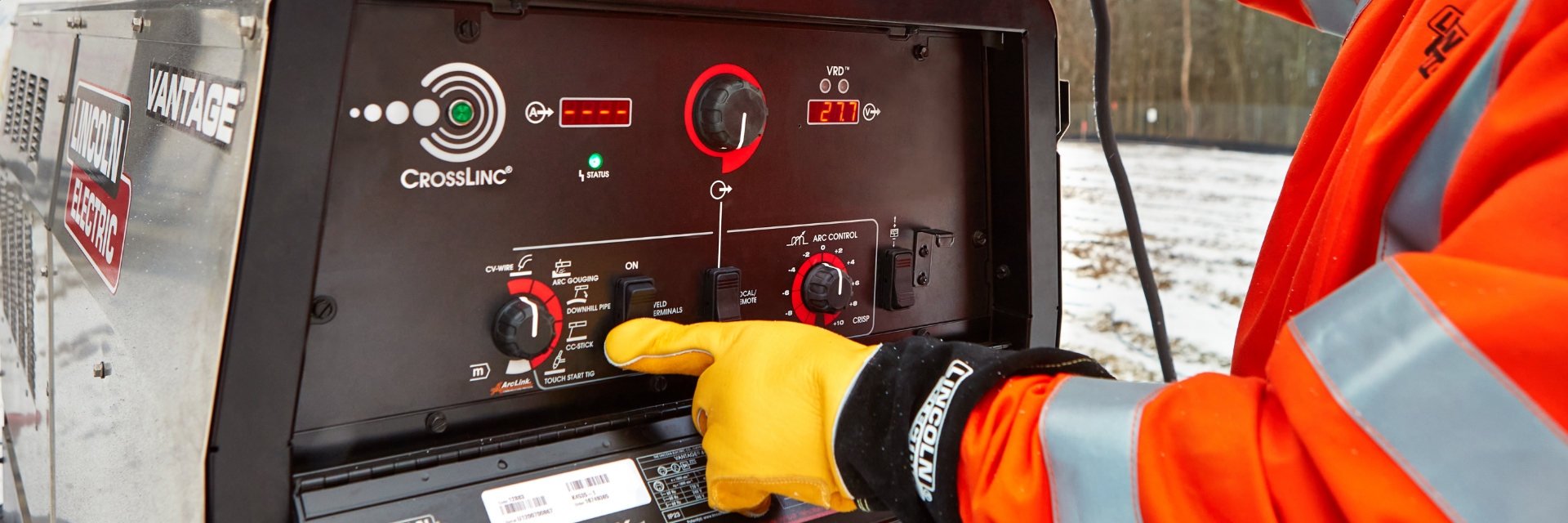
PRODUCT STEWARDSHIP
We are focused on advancing sustainability in our customers' operations and designing solutions to support de-carbonization across the end markets we serve. Our product stewardship initiatives focus on improving the design, manufacturing, packaging, and transportation of our products to improve customer safety, increase recyclability, and reduce our products' overall carbon footprint.
Our chemical information system (CIS) is a key enabler of our global compliance strategy. For consumable products, the information in our CIS—which includes hazardous product ingredients and potential fume constituents—is incorporated into product compliance specifications and outlined in Globally Harmonized System Safety Data Sheets (GHS SOS), label templates, and safe use guidelines. Search for Welding Safety Data Sheets (lincolnelectric.com)
We comply with the European Union's (EU) Registration, Evaluation, Authorization, and Restriction of Chemicals (REACH) regulations. Where required and relevant, consumable substances and mixtures manufactured in and imported into the EU by Lincoln Electric have been registered in the EU. Similarly, our electrical and electronic equipment complies with applicable global regulatory requirements, such as the European Union's Restriction of Hazardous Substances (ROHS) Directive.