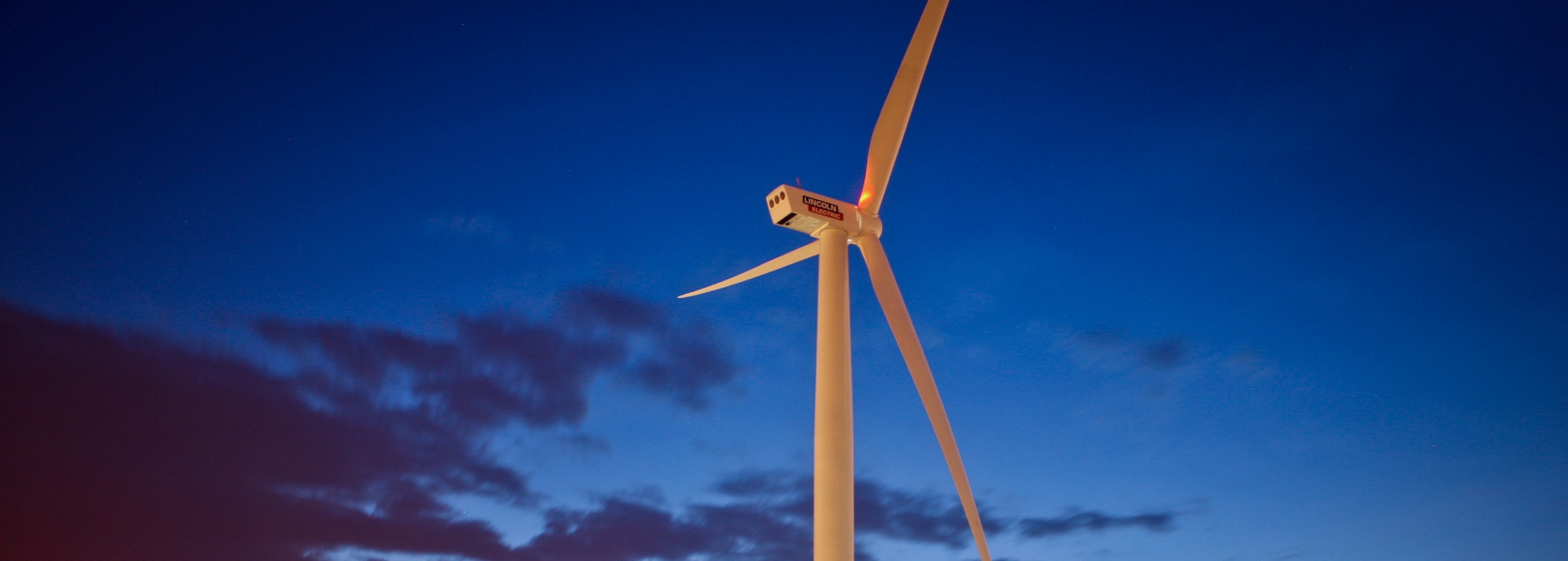
Operational
We strive to improve our performance annually across key environmental metrics to deliver superior value to all stakeholders. Our goals and practices associated with greenhouse gas emissions, energy intensity, recycling, and water use demonstrate our commitment to best-in-class performance and reducing our operational footprint.
GREENHOUSE GAS EMISSIONS & ENERGY INTENSITY
We are committed to reducing our carbon footprint through the reduction of greenhouse gas (GHG) emissions. In 2023, we reduced absolute Scope 1 and 2 thanks to continued investment in energy Efficiency projects within our operations. Energy intensity — the total amount of energy consumed per labor hour worked — is also one of our key metrics with improvement goals.
Absolute Metric Tons CO2e of GHG

in scope 1 and scope 2 GHG emissions from 2018 baseline
total tons CO2e from 2018 baseline to 2023
- Scope 1
- Scope 2
RECYCLING & LANDFILL AVOIDANCE
We aspire to achieve zero waste from our operations. Our waste management program prioritizes a “reduce, reuse, and recycle” approach to divert waste from landfills, leverage waste as a resource, and increase recycling in our operations.
This includes expanding the use of our waste as a feedstock for third parties and introducing collection and handling systems that allow us to capture and reuse materials. We measure the percentage of all waste that we can reuse or recycle, the percentage of permissible waste1 that can be diverted from landfills, and the percentage of hazardous waste.
- Permissible waste is waste that is non-hazardous (per the local country definition).
Total Waste Recycling & Landfill Avoidance
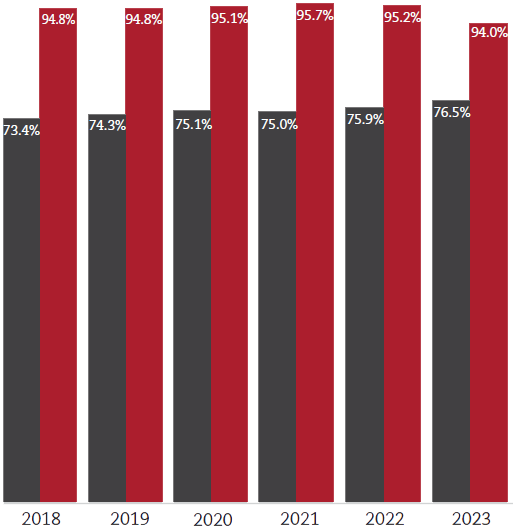
- Total Waste Recycling Percentage (Including Metals)
- Landfill Avoidance Percentage
WATER MANAGEMENT
Water is an important natural resource and we acknowledge our responsibility to manage water carefully. Water is predominantly used in our consumable manufacturing processes. We monitor and measure absolute water use and water intensity (cubic meters of water used per hour worked).
Water Usage (Cubic Meters)

from 2018 baseline to 2025
from 2018 baseline to 2023
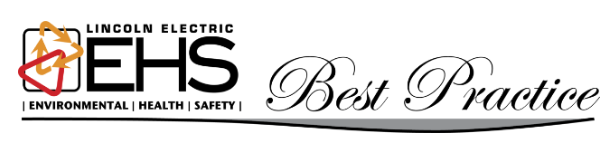